Benefits of Closed-loop Systems in Robotic Motor Control
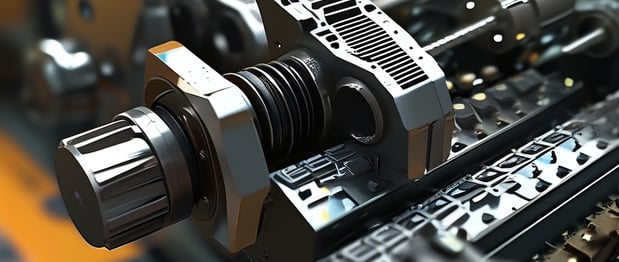
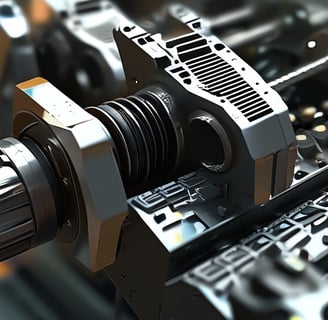
Imagine you’re working on a high-stakes robotics project, where even a slight misalignment can mean failure. Your team has spent months perfecting the design, but as soon as the robotic arm moves, you realize the motor control system isn’t keeping up. The errors start piling up, and the project risks going over budget and off schedule. This is where the difference between an open-loop and a closed-loop system becomes strikingly clear.
In the world of robotics, precision and real-time responsiveness are essential. For engineers and project managers who seek efficiency in their motor control systems, closed-loop systems offer a powerful solution. Let's dive into the advantages of closed-loop systems in robotic motor control and explore why they're becoming a staple in modern automation.
What is a Closed-loop System?
In motor control, a closed-loop system is designed to continuously monitor and adjust the performance of a motor based on feedback. Unlike open-loop systems, which function on a set of predefined instructions with no ongoing adjustment, closed-loop systems rely on real-time data to make automatic corrections.
For example, when a robotic motor's speed or position deviates from the intended path, sensors in a closed-loop system detect the error and relay that information back to the controller. The controller then adjusts the motor’s input to correct the deviation, maintaining precision throughout the process.
Key Benefits of Closed-loop Systems
1. Improved Accuracy and Precision
Closed-loop systems provide unparalleled accuracy in robotic applications by constantly monitoring and adjusting the motor's output. A study by the IEEE shows that closed-loop control systems can reduce positional error rates by up to 90% compared to their open-loop counterparts. For robotics engineers working in environments that demand high precision—such as in manufacturing or medical devices—this level of control is crucial.
2. Real-time Feedback for Enhanced Control
The ability to provide real-time feedback is one of the most significant advantages of closed-loop systems. This feedback ensures that any deviations from the target are quickly corrected. In automated systems, such as robotic arms assembling intricate components, this real-time adjustment is vital to avoid delays and maintain operational efficiency.
Consider how TurboFlys brushless direct drive motor integrates seamlessly into closed-loop systems, providing real-time feedback for optimal motion control. This makes it ideal for applications requiring precise adjustments, such as robotics used in high-precision environments like aerospace and automotive industries.
3. Reduced Error Rates
Closed-loop systems drastically reduce the margin for error, ensuring that the motor performs within the specified parameters. According to a report from the Control System Society, closed-loop motor systems can cut error rates by 50% to 70%, translating to more reliable and consistent operations. This reduced error rate is particularly beneficial in industries like automation and robotics, where even the smallest deviations can lead to costly downtimes or compromised product quality.
4. Energy Efficiency and Cost Savings
By continuously optimizing motor performance, closed-loop systems often consume less energy. They only provide the necessary amount of power based on real-time feedback, reducing waste and improving energy efficiency. Over time, this translates to cost savings, especially in large-scale automation projects where energy consumption is a significant concern.
5. Enhanced System Longevity
The ability to operate efficiently and with fewer errors reduces wear and tear on robotic motors, increasing their operational lifespan. A motor system that experiences fewer positional deviations will endure less stress, extending its longevity and decreasing maintenance costs. This long-term benefit is crucial for project managers looking to minimize operational costs over the life of their robotic systems.
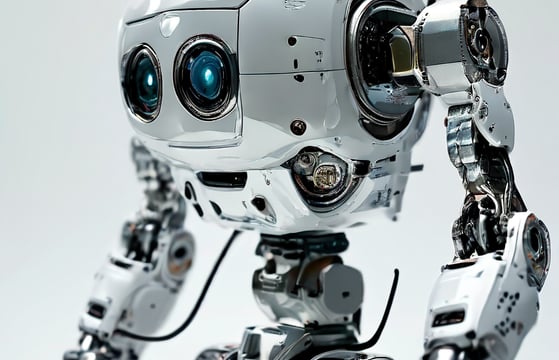
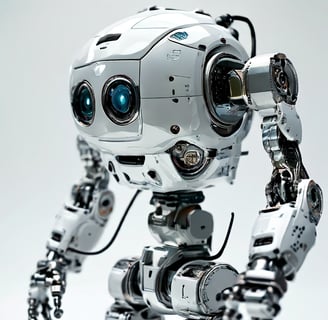
The Role of TurboFlys Brushless Direct Drive Motors in Closed-loop Systems
TurboFlys brushless direct drive motors are an excellent example of how closed-loop control can be applied effectively. With their precision engineering and ability to provide real-time feedback, these motors are ideal for applications where high accuracy and minimal error are non-negotiable. Whether you're building robots for industrial automation or high-end consumer electronics, integrating TurboFlys motors into your closed-loop system ensures optimal performance and long-term reliability.
Conclusion
Closed-loop systems are transforming the way we think about robotic motor control, offering engineers, project managers, and automation specialists a reliable solution for increasing precision, reducing errors, and improving efficiency. As more industries adopt automation, the need for accurate, real-time control will only continue to grow. Whether you’re overseeing the development of a precision robotic arm or ensuring the smooth operation of an automated manufacturing line, integrating closed-loop systems into your motor control strategy is a wise investment.
By leveraging the power of closed-loop technology—along with high-performance motors like those from TurboFlys—you can achieve the accuracy, efficiency, and longevity that modern robotic systems demand.