Open-Loop vs. Closed-Loop Systems: Which is Right for Your Robot?
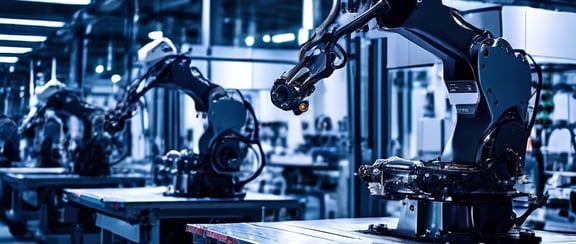
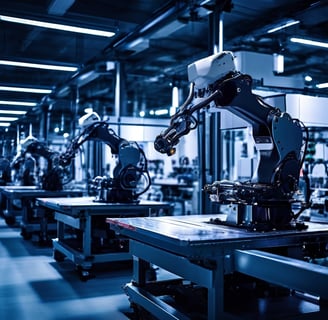
In the world of robotics, precision and control can make or break your project. Imagine a robot arm on an assembly line tasked with welding components. Every movement it makes has to be accurate, otherwise, a slight error could mean production delays or costly material waste. The type of control system you choose—whether open-loop or closed-loop—can determine how smoothly and efficiently this process runs. The right system can lead to optimal performance, while the wrong one can result in inefficiencies, costly repairs, and even project failures.
Understanding the Basics: What are Open-Loop and Closed-Loop Systems?
At their core, both open-loop and closed-loop systems manage how your robot motors function, but they do so in very different ways.
Open-Loop System: In an open-loop system, the controller sends a signal to the motor, and the motor acts without receiving feedback. There’s no mechanism for self-correction if something goes wrong during execution. It's akin to setting a timer for your coffee machine—once it starts, it doesn’t adjust based on the water level or bean quality.
Closed-Loop System: Closed-loop systems, on the other hand, continuously monitor feedback from the motor (like speed or position) and adjust the output accordingly. It's like driving a car and making constant steering adjustments to keep it in the lane. This real-time feedback makes closed-loop systems more accurate and adaptive.
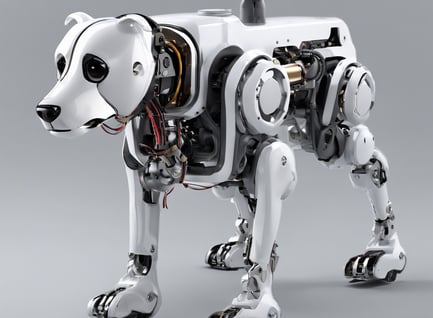
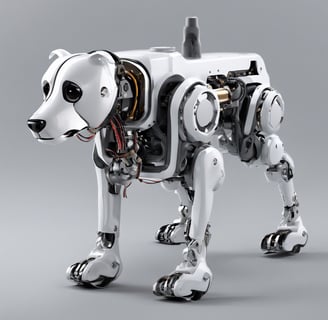
Performance Differences: Which Offers More Precision?
Open-Loop Systems: These systems are typically simpler and less expensive. For applications that don’t require high precision, such as basic movement or repetitive tasks where accuracy isn’t critical, an open-loop system may suffice. However, since they don’t correct for errors, open-loop systems are prone to inaccuracies over time, especially under varying loads or external conditions.
Closed-Loop Systems: Closed-loop systems excel in applications requiring precise control. For example, if your robot needs to lift varying loads or execute intricate movements, a closed-loop system will adjust motor power and speed based on real-time feedback. Studies show that closed-loop systems can reduce error rates by up to 90% in complex tasks compared to their open-loop counterparts.
Application Suitability: Which One Fits Your Robot?
The decision between open-loop and closed-loop systems largely depends on your robot's application and its performance requirements. Here are some key factors to consider:
Precision Requirements: If your robot is tasked with delicate tasks like surgical assistance, where minute errors can lead to significant consequences, a closed-loop system is a must. On the other hand, for tasks like warehouse item sorting or basic locomotion, an open-loop system could be more cost-effective.
Environmental Conditions: In environments with varying conditions (such as fluctuating temperatures or load changes), a closed-loop system provides the adaptability needed to maintain performance. Open-loop systems, by contrast, perform best in stable, predictable environments.
Budget Considerations: Closed-loop systems generally come with higher upfront costs due to the added complexity of sensors and feedback mechanisms. However, these costs are often offset by higher efficiency, reduced downtime, and lower long-term maintenance costs. For budget-conscious projects with less demanding precision needs, an open-loop system may still be a good choice.
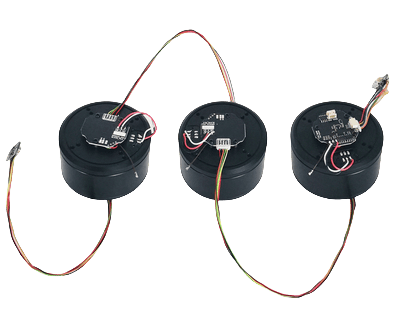
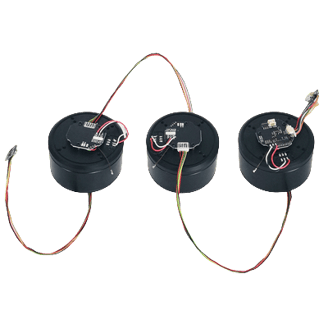
Real-World Example: TurboFlys Robot Hub Motor
Let’s take TurboFlys robot hub motor as an example. This hub motor is designed for versatility and high performance, which makes it suitable for both open-loop and closed-loop systems. For applications like autonomous navigation in robotics or precision movements in manufacturing, pairing this hub motor with a closed-loop system would offer superior control, real-time error correction, and efficiency. On the flip side, for simpler tasks where cost-effectiveness is key, an open-loop system paired with the TurboFlys motor can still deliver reliable performance without the added expense.
Statistics Highlighting the Impact of System Choice
A study conducted by Automation World revealed that robotics systems using closed-loop control improved performance accuracy by an average of 30% compared to open-loop systems in industrial applications. Additionally, companies reported a 25% reduction in downtime and a 15% increase in energy efficiency when upgrading from open-loop to closed-loop systems.
Moreover, Robotics Business Review noted that 65% of robotics engineers prefer closed-loop systems for high-stakes applications, while only 35% opt for open-loop systems for simpler, repetitive tasks.
Which System Should You Choose?
Ultimately, the choice between open-loop and closed-loop systems hinges on the specific needs of your project:
If cost-efficiency and simplicity are your primary concerns, and your robot operates in a stable, predictable environment, an open-loop system could be the right choice.
If your robot needs to operate in dynamic environments or perform tasks that demand high precision, real-time feedback, and error correction, investing in a closed-loop system will pay off in the long run.
Conclusion: Weighing Your Options
Deciding between open-loop and closed-loop systems is a crucial step in building an efficient, high-performing robot. While open-loop systems offer simplicity and cost savings, closed-loop systems provide the precision and adaptability needed for more complex and critical applications. By understanding the pros and cons of each system and matching them to your specific project requirements, you can ensure that your robot achieves the best possible performance.
For more advanced applications requiring high precision and real-time feedback, consider pairing your robot with TurboFlys robot hub motors and a closed-loop system for optimal performance.