High Efficiency of Direct Drive Motors: Key Benefits Explained
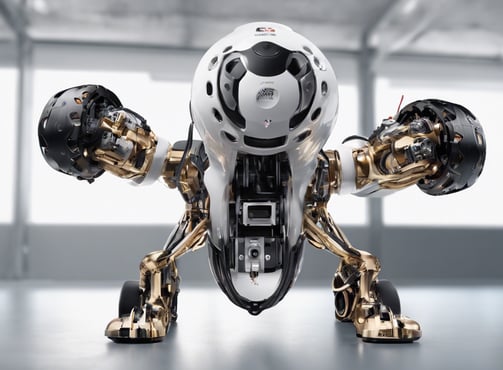
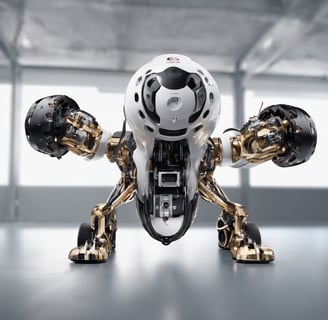
In today's fast-paced, innovation-driven world, efficiency is the new currency. Whether you're leading a robotics project, managing industrial automation, or handling procurement for high-performance machinery, optimizing motor systems can make or break your success. Imagine cutting down on machine downtime, reducing energy consumption, and increasing precision—without compromising on power. Enter the direct drive motor, a game-changer in efficiency and reliability.
The Shift Towards Direct Drive Motors
The engineering landscape is rapidly shifting towards direct drive motors (DDMs) for their unparalleled benefits. Unlike traditional motors, which rely on gearboxes or belts, DDMs connect directly to the load. This design eliminates unnecessary mechanical components, drastically reducing energy loss and maintenance requirements.
In fact, studies show that direct drive motors can increase energy efficiency by up to 30% compared to conventional motor systems. The lack of intermediary parts means fewer points of failure, translating to maintenance savings of 20-40% over the motor’s lifetime. For project managers and engineers, these numbers directly impact your bottom line—less downtime, fewer repairs, and more reliable performance.
Why Efficiency Matters in Robotics and Automation
Efficiency isn't just about energy savings; it’s about improving the overall performance of your systems. Robotics engineers, in particular, require motors that offer precise control for delicate operations. DDMs deliver just that. The direct connection to the load ensures smooth, accurate movements with minimal backlash, making them ideal for applications that demand high precision, such as robotic arms, gimbal systems, and automated manufacturing processes.
TurboFlys’ direct drive brushless motors are a perfect example of this innovation at work. Their high torque-to-weight ratio and exceptional energy efficiency make them ideal for industries ranging from robotics to factory automation. By integrating TurboFlys DDMs into your project, you can expect enhanced system reliability and reduced operational costs—two factors every procurement officer values.
Key Benefits of Direct Drive Motors
Improved System EfficiencyThe absence of gears or belts means less friction and wear, which translates into higher energy efficiency. DDMs can convert more electrical energy into mechanical energy, reducing power consumption and operational costs.
Reduced MaintenanceFewer mechanical parts mean fewer breakdowns. Direct drive motors require minimal upkeep, saving your team both time and money. This reduction in maintenance not only decreases costs but also increases machine uptime, which is critical for production lines.
Precision ControlIn robotics and automated systems, precision is everything. Direct drive motors offer high-resolution control without the mechanical lag caused by gear systems. This is particularly beneficial in applications like CNC machining or robotic surgery, where even the slightest inaccuracy can lead to costly errors.
Quiet OperationDDMs run more quietly than traditional motors, making them suitable for noise-sensitive environments like medical facilities or research labs.
Real-World Application: Why TurboFlys Direct Drive Motors Excel
In an industry where precision and efficiency are paramount, TurboFlys direct drive brushless motors stand out. Their advanced design allows for seamless integration into robotic systems, providing engineers and project managers with the tools they need to meet high-performance demands. TurboFlys motors not only offer improved torque and speed but also maintain high efficiency, even under heavy loads. For procurement officers, this means fewer replacements, less maintenance, and a significantly lower total cost of ownership.
Statistics That Matter
30% Increase in Energy Efficiency: Studies have shown that DDMs outperform traditional motors in energy conversion, making them a more sustainable choice in the long term.
40% Reduction in Maintenance Costs: By eliminating intermediary components like gears and belts, DDMs drastically cut down on wear-and-tear expenses.
Up to 20% Higher Torque Output: Direct drive motors deliver better performance, especially in applications where high torque is essential for precision and control.
Making the Right Choice
For robotics engineers, project managers, and procurement officers, choosing the right motor isn’t just about meeting technical requirements—it’s about future-proofing your systems. Direct drive motors offer an ideal balance of efficiency, precision, and reliability. Whether you’re designing complex robotic systems or optimizing factory operations, DDMs can enhance your performance metrics while reducing long-term costs.
TurboFlys’ direct drive brushless motor is a prime example of how these motors can elevate your project. From improved energy efficiency to reduced maintenance, TurboFlys offers the perfect solution for those looking to maximize performance without the hassle of constant repairs or replacements.
Conclusion: Investing in Efficiency
The future of motor technology lies in high-efficiency solutions like direct drive motors. By eliminating inefficiencies and mechanical redundancies, DDMs provide robotics engineers and project managers with the precision and reliability they need to succeed. For procurement officers, the long-term savings on maintenance and energy consumption make DDMs a cost-effective choice.
If you're ready to take your systems to the next level, consider integrating TurboFlys direct drive brushless motors into your design. Their exceptional performance, coupled with long-term cost benefits, makes them the ideal solution for any high-efficiency application.