Direct Drive DC Motors in Semiconductor Manufacturing
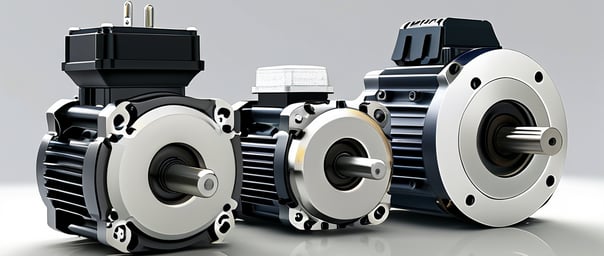
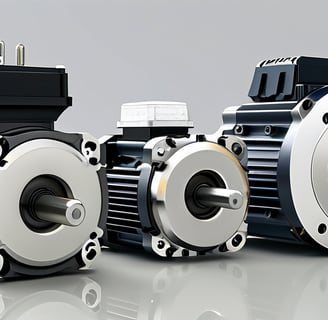
Introduction: A Quest for Perfection in Microelectronics
Imagine standing at the heart of a cutting-edge semiconductor fabrication facility, where every operation demands extreme precision, from aligning tiny wafers to positioning components within a hair's breadth. Semiconductor engineers, production managers, and equipment designers face relentless pressure to meet these demands for ever-higher precision and efficiency—ensuring that every millisecond counts and each micron is in place. In this high-stakes environment, direct drive DC motors are more than just a component; they are a critical enabler of precision, speed, and energy efficiency. But how do they achieve such transformative performance?
This article explores the essential role of direct drive DC motors in semiconductor manufacturing, highlighting their impact on efficiency and precision, and how TurboFlys brushless direct drive motor fits seamlessly into this narrative of progress.
The Need for Precision and Efficiency in Semiconductor Manufacturing
The semiconductor industry’s complexity goes beyond typical manufacturing processes. Operations such as wafer alignment, lithography, and chemical vapor deposition are executed in cleanroom environments with minute tolerances. A single misalignment or error can lead to waste, quality compromise, and lost production time.
Statistics from industry studies reveal that semiconductor manufacturing downtime costs can reach up to $100,000 per hour, a daunting figure that underscores the need for equipment capable of maximizing productivity. This is where direct drive DC motors, renowned for their torque control and precision, emerge as an ideal choice. In fact, research shows that direct drive motors can reduce cycle times by 15-30% in semiconductor applications, directly contributing to cost savings and increased throughput.
Why Direct Drive DC Motors? Key Benefits for Semiconductor Applications
In semiconductor manufacturing, high torque and low-speed stability are vital, and direct drive DC motors shine in both areas. Here’s how they meet the industry's specific demands:
Exceptional Precision with Minimal BacklashDirect drive DC motors operate without gears, which eliminates backlash—the unwanted play within the motor that can disrupt positioning accuracy. This gearless design ensures that positioning accuracy remains within microns, making these motors a top choice for wafer handling and lithography.
Increased Efficiency and Reduced MaintenanceDirect drive motors convert electrical energy into mechanical energy more efficiently than geared motors. Studies indicate that direct drive motors offer up to 20% energy savings compared to traditional motor setups, a significant advantage in a sector where energy costs are continually scrutinized. Additionally, their simplified design translates to fewer wear points and extended maintenance intervals, a welcome relief for production managers aiming to minimize downtime.
High Torque at Low SpeedsIn processes like chemical vapor deposition, precise control over low-speed operations is essential. Direct drive motors provide this capability with consistent torque output, ensuring smooth, accurate control even at lower speeds. This benefit is particularly valuable in processes requiring meticulous speed adjustments, such as wafer handling and etching.
Reduced Noise and VibrationIn a manufacturing setting where even minute vibrations can disrupt operations, direct drive motors help maintain the stability needed for high-precision tasks. By producing minimal noise and vibration, they safeguard the delicate processes within semiconductor facilities, especially in tasks involving photolithography.
TurboFlys Brushless Direct Drive Motor: Supporting Advanced Semiconductor Production
When choosing a direct drive motor, considering options that offer durability, high efficiency, and precision positioning is key. TurboFlys brushless direct drive motor aligns perfectly with these needs. Its brushless design minimizes wear and extends the motor's operational lifespan, a critical factor in semiconductor manufacturing where equipment must deliver reliable performance over long durations. Its compact design also allows for easy integration into production lines without taking up valuable space.
TurboFlys motor provides smooth and reliable operation across a range of speeds, ideal for tasks like wafer alignment and substrate handling, where precision is paramount. By leveraging advanced torque control, TurboFlys motor can enhance productivity and contribute to lower overall operating costs—a crucial advantage in the cost-sensitive semiconductor sector.
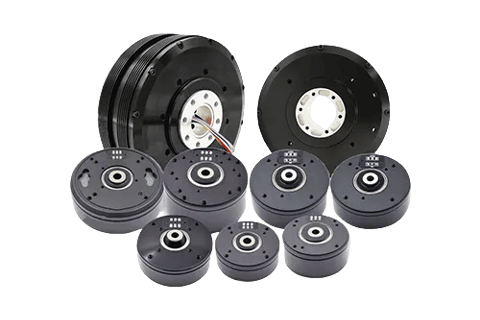
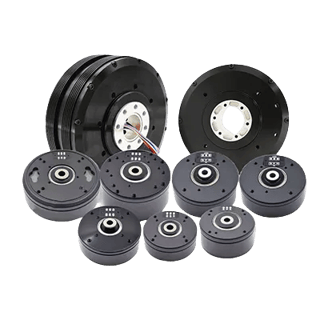
Applications of Direct Drive DC Motors in Semiconductor Manufacturing
Direct drive DC motors are invaluable in a variety of semiconductor manufacturing stages:
Wafer Processing and Handling: With no backlash, these motors guarantee highly accurate positioning, vital for aligning wafers during lithography.
Etching and Deposition: Their stable torque at low speeds ensures uniformity during deposition processes, maintaining consistent quality across production runs.
Testing and Inspection: Direct drive motors provide smooth motion and positioning for delicate inspection tasks, ensuring that components are aligned and inspected with extreme accuracy.
Embracing Direct Drive DC Motors: Future Growth in Semiconductor Manufacturing
As the demand for semiconductors grows, manufacturers are increasingly investing in direct drive motor technology to support efficient, precise production. The semiconductor equipment market itself is projected to reach $107 billion by 2025 as companies seek technology that can reliably meet their needs for quality and efficiency.
Direct drive DC motors not only fulfill current demands but are also adaptable to advancements in manufacturing. Their modular design allows for future upgrades, meaning production managers and equipment designers can be confident in their long-term utility.
Conclusion:
For semiconductor manufacturing to keep pace with technological demands, precision and efficiency are non-negotiable. Direct drive DC motors offer a viable, long-term solution, eliminating mechanical limitations associated with gear-based systems, reducing maintenance, and increasing throughput. TurboFlys brushless direct drive motor exemplifies how these motors can seamlessly integrate into semiconductor applications, meeting industry standards while providing unparalleled reliability.
By investing in direct drive DC motors, semiconductor facilities are not only optimizing for today but also future-proofing their processes to handle the innovations of tomorrow.