Cost Considerations for Direct Drive Motors: Optimize Performance
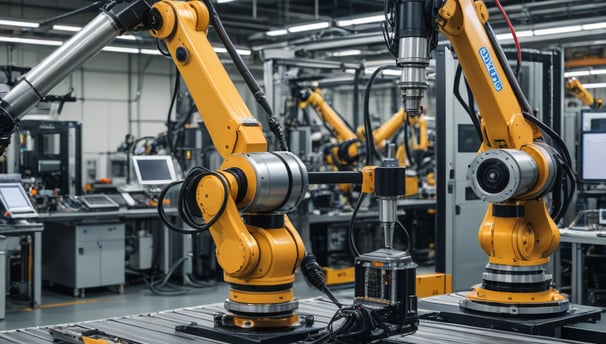
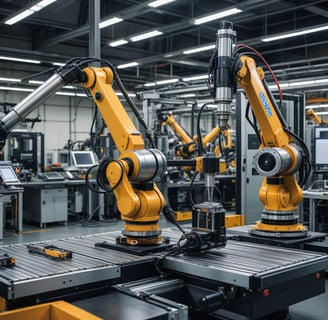
In the fast-paced world of robotics and automation, every decision impacts not only immediate performance but also long-term efficiency. Imagine the challenge faced by a robotics project manager: the pressure to choose the right motor that balances high performance with cost-effectiveness. The motor you choose could be the difference between staying within budget or facing unexpected operational costs down the road. So, how do you weigh the cost considerations of direct drive motors and make a decision that works for your project?
This article will guide you through the key cost drivers that influence the price of direct drive motors, providing actionable insights to help you make the most informed choice. By understanding the factors behind motor costs, you can optimize your selection process and achieve long-term savings without sacrificing performance.
Understanding the Cost Drivers of Direct Drive Motors
1. Motor Specifications: The Foundation of Cost
The technical specifications of a motor are the first and most significant factors influencing its cost. Direct drive motors, known for their high precision and torque, often come with higher upfront costs compared to conventional motors. Key specs such as power output, torque, and size directly affect pricing. For instance, high-torque motors, such as those used in heavy-duty industrial robots, will naturally be more expensive than those for lighter applications.
Statistical Insight: According to industry reports, up to 60% of a motor's cost is determined by its torque and power specifications. Engineers must assess their project's exact requirements to avoid overspending on unnecessary capabilities.
2. Integration Costs: The Hidden Expenses
Beyond the motor itself, there are integration costs to consider. Direct drive motors often require precise installation and calibration with other mechanical systems, which can incur additional labor and customization expenses. While direct drive motors offer smoother operation and less maintenance compared to traditional motors, ensuring seamless integration with your system can add up quickly.
Practical Example: TurboFlys direct drive spindle motor is designed for easier integration, minimizing the need for extensive calibration. Its design reduces setup time, helping project managers avoid additional labor costs during the installation phase.
3. Long-Term Operational Savings: The Trade-Off
Though direct drive motors typically involve a higher initial investment, they often deliver significant savings in the long run. With fewer mechanical parts to wear out, these motors reduce the need for maintenance and replacements, improving your project's ROI. Additionally, their high efficiency translates into lower energy consumption over time, which can dramatically cut operating costs.
Statistical Insight: Studies show that direct drive motors can lower energy consumption by 10-30% compared to traditional motors, leading to substantial savings over the motor’s lifetime.
4. Application-Specific Customizations
Tailoring a direct drive motor to specific project needs, such as adjusting for environmental conditions or specialized operational requirements, will affect the overall cost. Custom features like enhanced cooling systems, specialized coatings, or unique housing for harsh environments can drive prices up but are often worth the investment for critical applications.
Balancing Cost and Performance
When selecting a motor, it's essential to evaluate not just the upfront price but the long-term value it will bring. By understanding motor specifications, integration costs, and potential savings, you can make an informed decision that optimizes both performance and cost-efficiency.
Key Takeaway: Selecting a motor like TurboFlys direct drive spindle motor, which offers easy integration and long-term operational savings, can help you strike the right balance between cost and performance. Without overspending on unnecessary features, this motor provides a practical solution for high-precision robotics applications, ensuring both efficiency and affordability.
Conclusion: Smart Decisions Lead to Sustainable Success
The cost considerations for direct drive motors go beyond the initial purchase price. By factoring in specifications, integration, and operational savings, you can make a choice that ensures both immediate success and long-term efficiency. With the right motor selection, your project can achieve high performance without breaking the budget.