Balancing Precision and Power: Key Motor Specs for Robotics
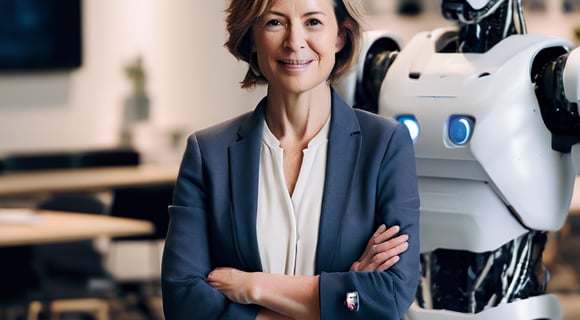
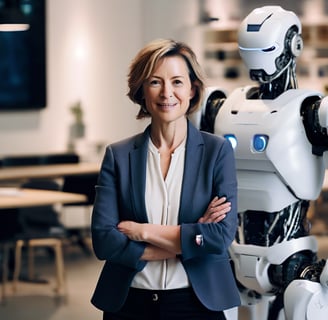
In the fast-evolving world of robotics, selecting the right motor is crucial to balancing precision and power. Whether you're building a high-speed robotic arm for assembly lines or designing an autonomous mobile robot, the motor you choose plays a pivotal role in your system’s overall performance. But how do you find the ideal motor without getting lost in technical jargon?
This article is here to guide you, offering clear, actionable insights on key motor specifications to help you optimize motor selection. Tailored for robotics engineers, project managers, and decision-makers in automation, this guide focuses on what matters most: balancing precision and power in robotic applications.
Understanding the Balance of Precision and Power
The success of any robotic system depends on two main factors:
Precision: The ability of the motor to position the robot or part accurately within a defined tolerance.
Power: The motor’s capacity to deliver the required torque or force to move a load, especially under varying conditions.
While these two factors are often seen as opposing forces—more power can sometimes compromise precision, and vice versa—the right motor can achieve both. Let’s explore the critical specifications that influence this balance.
Key Motor Specifications to Consider
1. Torque: The Foundation of Power
Torque is the motor’s ability to produce rotational force. In robotics, torque is crucial for moving loads, whether you're lifting objects with a robotic arm or powering a drive system. Selecting a motor with insufficient torque can lead to underperformance, while too much torque may result in wasted energy or reduced efficiency.
Practical Insight: Consider both continuous torque and peak torque. Continuous torque reflects the motor’s capacity to run efficiently over long periods, while peak torque indicates how much force the motor can provide in short bursts.
2. Speed: Finding the Right Balance
Motor speed is how quickly the motor can rotate, typically measured in RPM (revolutions per minute). In robotic applications, speed must be optimized for the specific task. High-speed motors are ideal for quick, repetitive tasks, while lower speeds allow for greater control and precision.
Actionable Tip: Assess the motor's speed in relation to the task. If you need precise, delicate movements—such as in medical robotics—opt for a motor that provides finer control at lower speeds.
3. Encoder Resolution: Precision Under Control
Encoder resolution defines how accurately the motor can measure its position. A high-resolution encoder enables finer movements, which is vital in applications like robotic surgery or semiconductor manufacturing, where even slight deviations can lead to costly errors.
What to Look For: High encoder resolution is critical when accuracy matters most. Ensure that the motor you choose includes an encoder that matches the precision demands of your project.
4. Power Efficiency: More Than Just Savings
In robotics, power efficiency is about more than reducing energy costs—it impacts the overall performance and longevity of the system. Motors that operate efficiently generate less heat and require less cooling, making them suitable for continuous use in demanding environments.
Optimization Insight: Choose a motor that strikes a balance between power output and energy consumption. For long-running applications, efficiency can significantly extend the lifespan of both the motor and the overall robotic system.
5. Inertia: Controlling Momentum
Inertia refers to a motor’s resistance to changes in motion. High-inertia motors are excellent for steady movements, but they may struggle with rapid changes in speed or direction. For robotics systems that need fast responses, such as robotic arms that handle delicate tasks, low-inertia motors are preferred.
Actionable Advice: When selecting a motor, match the inertia to the application. Low-inertia motors are ideal for fast-moving systems that require frequent stops and starts, while high-inertia motors are suited for applications requiring smooth, continuous movement.
Practical Example: TurboFlys Brushless Direct Drive Motor
To illustrate the practical application of these specifications, let’s consider TurboFlys’ brushless direct drive motor. It offers high torque and precision, making it an excellent choice for robotic applications that require fine control without sacrificing power. Whether you're working on industrial robots or automation systems, this motor strikes the perfect balance between performance and efficiency.
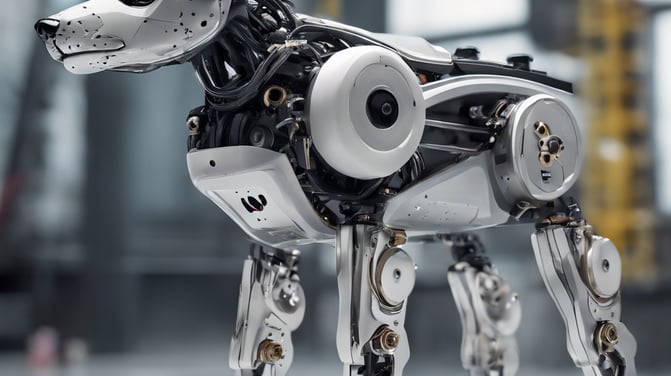
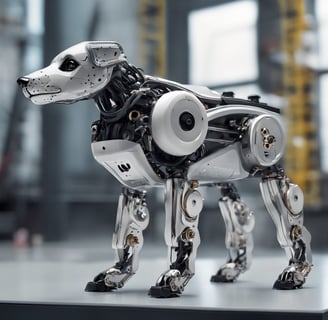
Conclusion: Making Informed Motor Selections
Selecting the right motor for your robotics application doesn't have to be overwhelming. By focusing on key specifications—torque, speed, encoder resolution, power efficiency, and inertia—you can make well-informed decisions that optimize both precision and power.
Remember, every application is different. Understanding the unique demands of your project and how each motor specification affects performance will ensure you choose a motor that not only meets but exceeds your expectations.
This balanced approach will help you achieve the perfect blend of precision and power, enabling your robotics systems to perform at their best.