An Introduction to Motor Controllers for Robotics
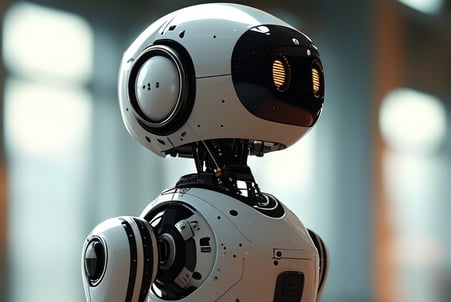
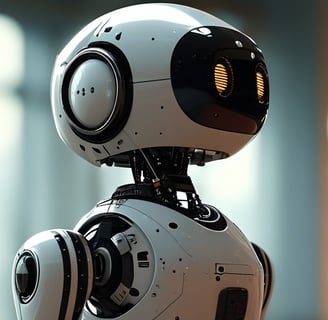
Imagine a world where robots can perform tasks with the precision of a surgeon and the strength of a titan. This is not the realm of science fiction but the reality of modern robotics, thanks to the advancements in motor controllers. For robotics enthusiasts and engineers, understanding the fundamentals of motor controllers is crucial to harnessing the full potential of robotic systems. In this article, we will delve into the key features and benefits of direct drive motor controllers, a technology that is revolutionizing the field of robotics.
The Rise of Robotics
The robotics industry is experiencing unprecedented growth. In 2022, over half a million industrial robots were installed worldwide, marking a 31% year-on-year growth rate since 2015. This surge in demand is driven by the need for precision, reliability, and efficiency in various industries. At the heart of this revolution are motor controllers, the unsung heroes that enable robots to move, manipulate, and interact with their environment.
What are Motor Controllers?
A motor controller is an electronic device that regulates the operation of motors in robotic systems. It manages the power delivery to the motors, allowing precise control over their speed, direction, torque, and position. This level of control is essential for tasks that require high precision, such as assembly, welding, and surgery.
Direct Drive Motor Controllers: The Game Changers
Direct drive motor controllers are a type of motor controller that eliminates the need for mechanical transmission elements like gearboxes and timing belts. This design simplifies the system, reduces maintenance requirements, and improves precision. Direct drive motors are characterized by their ability to produce high torque at low rotational speeds, making them ideal for applications that require precise control or heavy load movement.
Key Benefits of Direct Drive Motor Controllers
Enhanced Precision: Direct drive motors eliminate backlash and inertia mismatch, providing accurate and repeatable positioning.
Increased Reliability: With fewer moving parts, direct drive motors experience less mechanical wear, reducing downtime and maintenance costs.
Improved Efficiency: Direct drive motors convert electrical energy into mechanical energy with heightened efficiency, minimizing energy losses.
Cost Savings: By eliminating the gearbox, direct drive actuators can be produced at a lower cost, making them more accessible for various applications.
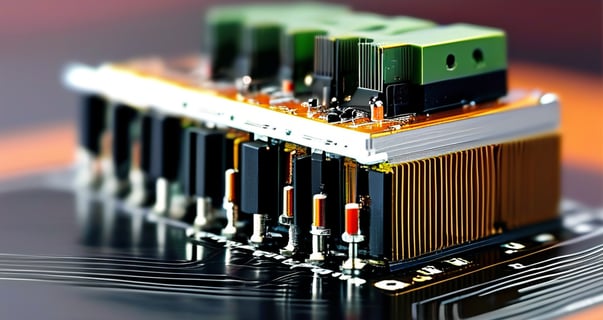
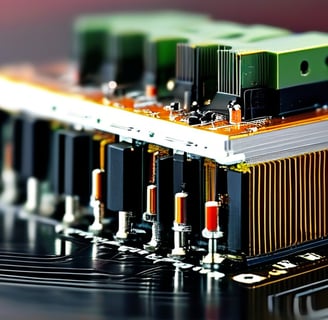
TurboFlys Direct Drive Motor Controller: A Case in Point
TurboFlys direct drive electric motors are a prime example of how this technology can offer high precision and reliability for manufacturers. Their motors are designed to provide the precise rotation speed required by applications, eliminating the need for transmission systems and ensuring smoother torque delivery.
Conclusion
In the world of robotics, motor controllers are the backbone of any robotic system. Direct drive motor controllers, in particular, offer a level of precision, reliability, and efficiency that is unmatched by traditional systems. As the robotics industry continues to grow, understanding the fundamentals of motor controllers will become increasingly important for robotics enthusiasts and engineers. By embracing direct drive technology, we can unlock new possibilities in robotics, from collaborative robots to high-speed spindles, and pave the way for a future where robots can perform tasks with unprecedented precision and power.